A sandblasting nozzle is generally a type of nozzle used with a sandblasting machine that blasts abrasive material through a hose and out of the nozzle at high pressure; it scrubs surfaces by blasting, removes fixed layers of material, and even etches artistic designs into hard materials such as wood and glass. Because of the pressure involved, sandblasting nozzles are constructed with durability and flow control in mind. As a result, they can come in various materials, shapes, sizes, and costs, each with its unique advantages and disadvantages. These include tough materials with varying strength or temperature tolerances, such as ceramic, tungsten carbide, and boron carbide. Nozzle valve types include conventional on/off valves, variable pinch valves, foot switches, shutoff valves, and PAB valves.
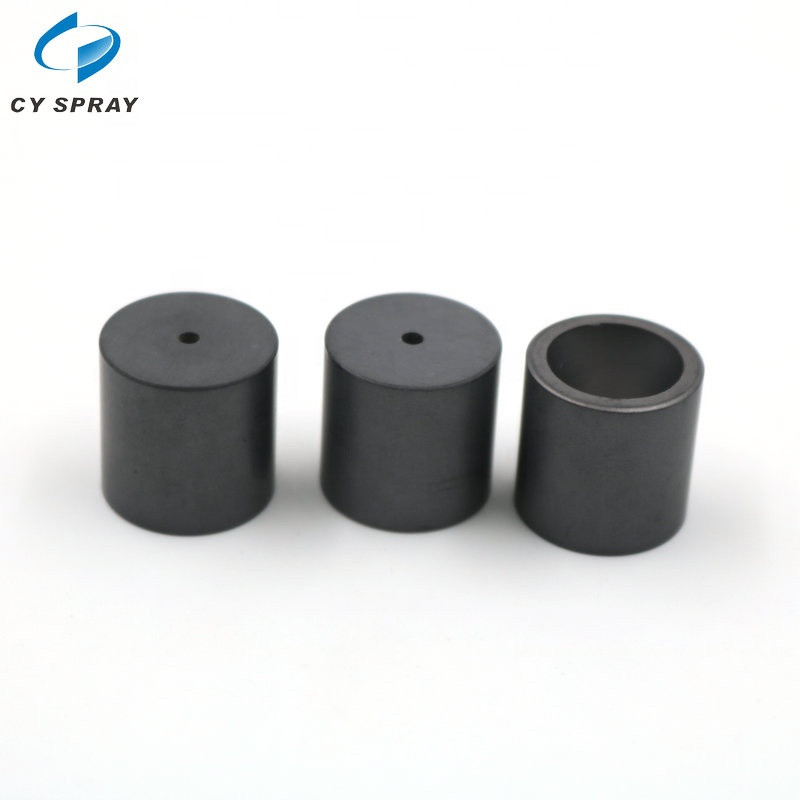
Ceramic blast nozzles exhibit rugged, inexpensive performance. Made of non-magnetic, rust-resistant materials, these nozzles perform well in the “all-or-nothing” category; effective against wear, they occasionally fail and require more frequent backup changes. Harder materials such as tungsten carbide and boron carbide cost more but offer greater durability, thermal conductivity, and lighter weight. Tungsten carbide is very hard and can be used to cut other metals. Boron carbide is the toughest ceramic; it is corrosion-resistant and has the longest life.
The most basic blasting nozzles have conventional on/off valves. Variable fixture nozzles allow better control of the abrasive flow. For greater freedom of movement, foot-switch operated nozzles allow the operator to perform finer work in confined areas, such as etching inside a cabinet. For safety reasons, the spring-loaded shutoff valve requires constant pressure on the squeeze handle to operate; a drop of water cuts off the flow of sand. Pickard Art Blast (PAB) model sandblasters enable fine variable trigger control for soft-touch artistic or industrial etching.
The higher-quality sandblasting nozzles wear evenly over time. They can usually be replaced by removing the set screw. Regarding nozzle size, wider holes allow for increased flow, just as fire hoses allow more flow than garden hoses. Other nozzle considerations include connection type, thread size, sheath material, and weight.
Abrasive blast nozzles are subjected to constant heavy pressure during their service life. Abrasive, coarse, and fine grit blasting requires careful attention to safety equipment and practices. Silicon dioxide dust can cause permanent damage to the respiratory system. In addition, the tremendous pressure caused by sandblasting can easily injure the operator or others. Operators should carefully check the condition of nozzles and equipment before use and minimize downtime by always changing them.
For custom sandblasting nozzles, please contact CYCO Spray, a professional sandblasting nozzle manufacturer.